Quality control is the systematic process of ensuring that all goods and services offered by a business meet or exceed the standards identified as necessary to attract, satisfy, and retain customers. This ongoing process of quality assessment and refinement helps companies to remain competitive over the long-term, as well as ensuring that the company has a reputation for providing customers with goods and services that are high in quality. As with many processes, there are ways to continually improve the level of quality control in just about every situation.
One of the most effective ways to measure and enhance quality control is to implement a process known as Total Quality Management, or TQM. Essentially, this approach involves looking at every aspect of the operation, beginning with the procurement of raw materials all the way through to delivery of finished goods to a customer. While this approach to quality control is intensive, it often can identify little issues that could mature into large problems and threaten the quality of the goods and services offered.
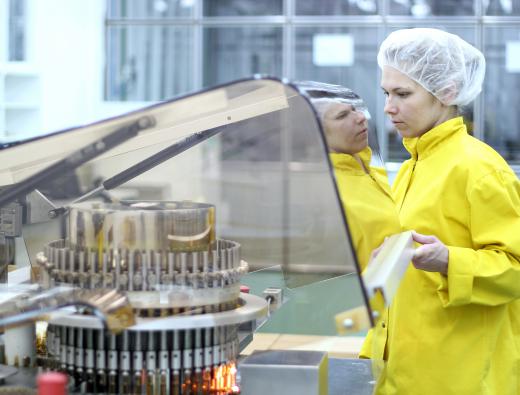
As part of TQM, a strategy known as statistical process control is often employed. This strategy seeks to not only determine what materials are used in the manufacturing process, but also how those materials are handled at each juncture along the way to the creation of a final product. This approach to quality management seeks to understand what factors may be causing some small amount of waste in terms of materials or time. By understanding what is currently taking place, it is possible to develop alternate procedures that would eliminate this waste of time or materials, thus allowing more products to be produced without compromising the quality of the finished goods.
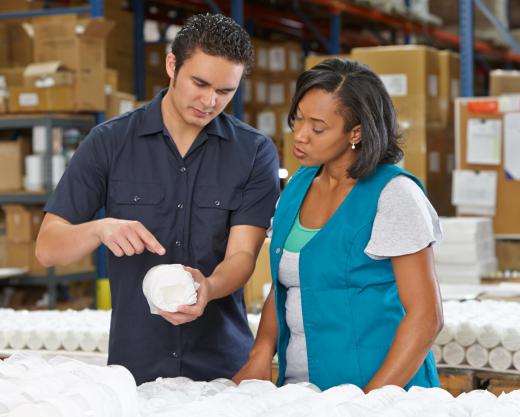
Because the measurement of quality standards is an ongoing process, there is always the chance of changing the methods of quality management from time to time. For example, if new equipment is ordered that can more efficiently handle the tasks formerly managed by machinery in two different departments, effective quality control may dictate that those two departments be merged into one entity. At the same time, increased production may mean that tasks once handled with ease in a single department may need to be segregated and become the function of two different departments.
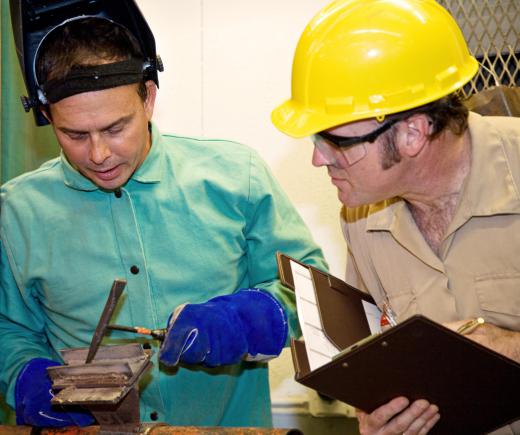
In most cases, measuring quality standards is not the sole responsibility of a quality assurance department or division. Instead, each department involved in the process of creating goods and services has certain standards it must meet. By breaking down the logical progression of materials through the manufacturing process, it is much easier to identify a flaw in the function of a given department and correct the problem before there is the chance of that one flaw creating more issues later in the process. The establishment and monitoring of standards at department level is just as important to quality control as overseeing the overall manufacturing process.
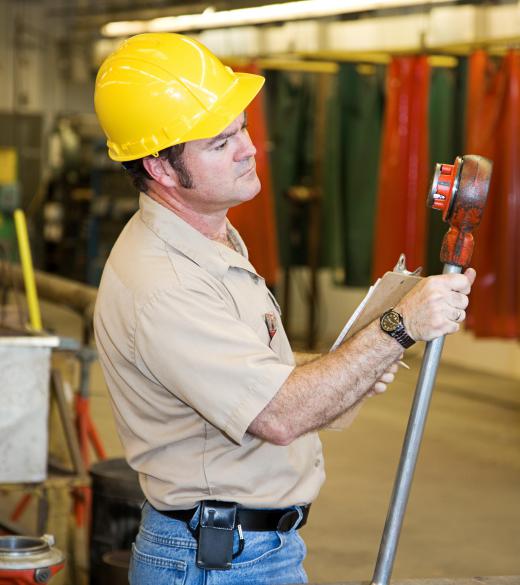
Computer technology has made it possible to use automated quality control tools to great effect. Tools of this type are constantly gathering and arranging data in formats that quality control and assurance personnel can evaluate. Use of this type of automated software can make it possible to identify potential quality issues before they have the chance to impact the customer, thus allowing the company to retain its good name as well as its client base.
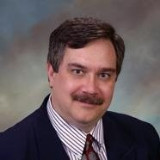